The Importance of Proper Heat Placement in Farrowing Facilities
Heat placement for young pigs is a critical component for getting animals started quickly and maintaining optimal health. In gestation and finishing, only one macro-environment is necessary because animals are of similar age and have similar temperature requirements.
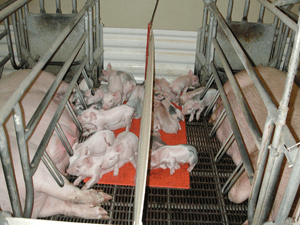
Heat mats, like Osborne’s Stanfield Heat Pad, are not likely to fail and cause a “no heat event” like heat bulbs often do when they burn out. A “no heat event” can lead to increased crush loss and scours.
Conversely, in farrowing, nursery, and wean-to-finish, a micro-environment must be maintained within the larger airspace. In farrowing, piglets must be kept from becoming chilled, which often leads to scours, more tail-enders, and less healthy, thriving piglets.
A draft-free zone of warm air in the piglet zone is most desirable. At 48 inches off the floor, temperature can be maintained at 68° F (20° C) , but at the floor, or in this piglet zone, a constant temperature of 80-90° F (27 – 32° C) is desirable for much of the farrowing turn, or until animals are older and have less need for supplemental heat.
There are two ways to provide supplemental heat to piglets: from the top-down or the bottom-up. Heat rises, so having heat under the piglets tends to be more practical and economical. Heat is not lost because the heat source is completely utilized by the litter. Bottom-up heat works well for farrowing and nursery animals. Radiant heat from above the animals works best in wean-to-finish. Top-down heat provides a zone of comfort for animals to go to the feeder, get a drink, and then lie back down under the heat source.
For pigs up to 21 days, heating pads are the preferred choice for many reasons. First, a farrowing stall is rectangular, and the pig heat mat fits logically in the creep area, creating a 6-inch gap between the heat source and sow.
When heat lamps are used, heat travels to the sow, and a warm zone to discourage piglets from getting too close to the sow is not provided. This exponentially increases the chances of laid-ons or crush losses.
Second, by utilizing pig heating pads, there is no chance of “blowing a bulb,” which frequently happens with heat lamps. From the time the farm employees leave the facilities in the afternoon, until they arrive back the next morning, animals could be without heat, thus almost assuring the development of scours problems, respiratory issues, and other health problems that cost producers several days’ performance to get animals caught up with the rest of the piglets in farrowing.
A pig heat mat gets its heat input from either electricity or hot water. Many farms in Europe have water lines in the creep area that heat the sloped floor to keep concrete creep areas warm and dry.
In the US, electricity to heat pads is predominantly used, because most producers have perforated floors without any concrete. Concrete in a farrowing stall is more difficult to maintain because it has the potential for harboring Coccidiosis bacteria in the pores of the concrete. Pig heating pads provide a solid surface, whereas a rubber mat is required under a heat lamp. Most producers add a drying agent to the solid surface where the heat is, and some will add a creep feed later in the turn to get piglets started on nursery feed, or to help the tail-enders get caught up.
Another major benefit of a heat mat is its shape: Pig heating pads maintain a larger, more spread-out heat source in the creep area. For litters over 12 pigs, a 5 foot mat is used to provide the recommended 0.33 square feet per piglet. In wean-to-finish, Dr. Hongwei Xin of Iowa State University recommends 0.5 square feet per pig1.
Heat lamps cannot accomplish these recommendations. In order to provide more intense heat, lamps must be lowered closer to the floor surface, thus decreasing the usable heated area. In turn, to provide a larger coverage area of heat, lamps must be raised, which decreases the intensity.
Also, only one electrical outlet is needed for every two stalls with a pig heat mat, whereas a plug is needed for each heat lamp. Maintaining an extra, unused outlet in the stall allows for the use of heat lamps for day one pig care. Lamps can then easily be removed after the litter is born, because most litters are born at night and a heat mat can then provide the animals’ heating requirements.
Centering the pig heating pads in the creep area keeps the piglets near the teat they’re nursing from, thus encouraging increased lactation. By also keeping the sow cooler, she is encouraged to eat more and be more comfortable. Frequently, sows that are too warm fidget and move around to find a cooler place to lie, which increases crush-losses.
Pig heating pads can be cleaned while in-place in the farrowing stall. They are fastened at each corner and meant to be a fixture in the stall. Scours and rotavirus concerns can be minimized by cleaning along the edges of the pads. A heat mat has years of useful life, unlike heat lamps which can sometimes last for just days.
Heat mats are only a receiver of information on how warm they should operate. For example, Osborne’s Stanfield® Heat Pads operate 30 degrees above room temperature. A controller that provides the desired temperature is recommended. By using controllers, heat can effectively be ramped-down as animals grow, thus extending even greater energy savings.
The payback for a system of the heat mat and controller is routinely within 14 months on systems using 21-day farrowing cycles. The electrical savings per year with 4-ft mats vs. 125 watt bulbs averages $56 per year per stall2.
How Much Can You Save?
Stop wasting money on inefficient heat lamps!
Enter your data below to see how much you could save!
Do you like what you see? With the addition of Osborne Heat Pad Controllers, your savings will increase even further! Call your Osborne Sales Representative or Osborne Customer Service to learn about increasing your energy savings by switching to heat pads.
* Illustration represents heat pads and heat lamps operating at 100% power. Assumes sows are moved to Farrowing Barn three days prior to farrowing and no “downtime” in between groups. Figures are based solely upon user’s entered information. Osborne Industries assumes no responsibility and makes no guarantees about actual monetary or energy savings. The information is to be used for illustration purposes only.
The biggest advantage of pig heating pads, however, is in the pre-wean mortality reduction. Several tests have been conducted and validate a 0.5 pig per litter increase with mats due to diminished crush loss. With weaned pigs annually averaging $34, saving 0.5 pig on 14 litters per year equals 7 pigs. There will be extra feed cost to produce more animals, but a greater reduction in crush losses means more marketable animals and more producer-profits in the end.
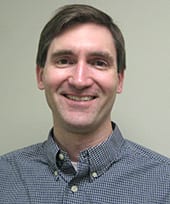
Brian Strobel, North American Sales Representative, Osborne Industries, Inc.
Brian Strobel, North American Sales Representative, of Osborne Industries, Inc., has extensive experience and knowledge of the swine industry. He has experience in swine management, construction, maintenance, and sales. A native of Ohio, Strobel holds a BS in Agricultural Systems from The Ohio State University, a Certificate of Civil Engineering Technology from Edison State College, an MS in Agriculture Engineering from Purdue University, and an MBA in Business Administration from Ohio University. He is also a certified professional engineer.
Osborne Industries, Inc., based in Osborne, Kansas, USA, is a 100% employee-owned company specializing in the manufacture and development of advanced livestock management equipment. Osborne’s Stanfield® Heat Pads were developed nearly 40 years ago and were the very first heat mats to be used in livestock production applications. Thousands of Osborne’s signature orange heat pads are used throughout the world. To learn more about Osborne Industries and their energy-saving pig heating pads, visit osbornelivestockequipment.com, or e-mail info@osborne-ind.com.
1 Zhang, Q. and H. Xin. 2002. Behavior of piglets in farrowing crates equipped with heat mats. Paper No. 024046, Am. Soc. Agric. Eng., St. Joseph, MI. 10 pp.
2 Calculations based on energy cost of $0.25/kWh